As the electric vehicle industry grows, the importance of having the battery technology to power the vehicles has grown in unison. Indeed, much of the value of the vehicles derives from their batteries, from the driving range they provide to the charging time of the battery.
New research from Stanford shows how AI can make batteries smarter by cutting the testing time of the batteries in production by up to 98%.
“In battery testing, you have to try a massive number of things, because the performance you get will vary drastically,” the researchers say. “With AI, we’re able to quickly identify the most promising approaches and cut out a lot of unnecessary experiments.”
Smart testing
The work, which was conducted in partnership with the Toyota Research Institute and MIT, aimed to charge an EV battery in less than 10 minutes that also maximizes the lifetime of the battery. The software developed by the team was able to decide in real-time whether specific charging methods were worth pursuing or ignoring. This cut the testing process down from one that would ordinarily take two years to just 16 days.
“We figured out how to greatly accelerate the testing process for extreme fast charging,” the researchers continue. “What’s really exciting, though, is the method. We can apply this approach to many other problems that, right now, are holding back battery development for months or years.”
This is a significant breakthrough, as traditionally fast charging is associated with poor lifespan. By using AI, the team were able to go through the same trial-and-error that humans would often utilize, but do so in greater volume, at faster speed, and with smarter iterations between each test.
The algorithm was able to spot factors that typically resulted in battery failure early on, so was able to prevent wasteful testing. The algorithm was also able to quickly hone in on the best approaches for testing, which again, reduced the wasted time and effort.
The AI’s solution was not to use the highest current at the beginning of the charge, but rather during the middle, which is counter-intuitive to many humans, and so often overlooked.
Buoyed by the early results, the team believe their approach could be applied to pretty much every piece of the batter development process, which could have significant implications for the electric vehicle industry.
“This is a new way of doing battery development,” they say. “Having data that you can share among a large number of people in academia and industry, and that is automatically analyzed, enables much faster innovation.”
To facilitate this transformation, both the algorithm and the data collection system used in the study will be made freely available for others to build upon.

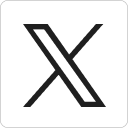



